Pick & Place
Pick & place applications are some of the easiest and quickest applications to deploy alongside machine tending. With a wide range of standard tooling available from the UR+ platform, it could be as simple as clipping on a gripper, bolting the Cobot to a stand and entering a simple program.
Remove Simple Repetitive Tasks
A common example of a pick and place application involves an operator being placed on a conveyor and then transferring product from the conveyor into a box all day. Usually, there would be several operators doing this.
This is a boring and repetitive task, with symptoms such as Repetitive Strain Injury (RSI) becoming a factor after prolonged work. You would need to fit the conveyor with a sensor, which triggers the pick of the robot. The robot would then transfer the product into the box.
This means you can reduce the number of staff working on the line, or if more work is required, you can also consider using additional labour. The operator can then focus on maintaining and running the line, e.g. removing full boxes or dealing with deformed products.
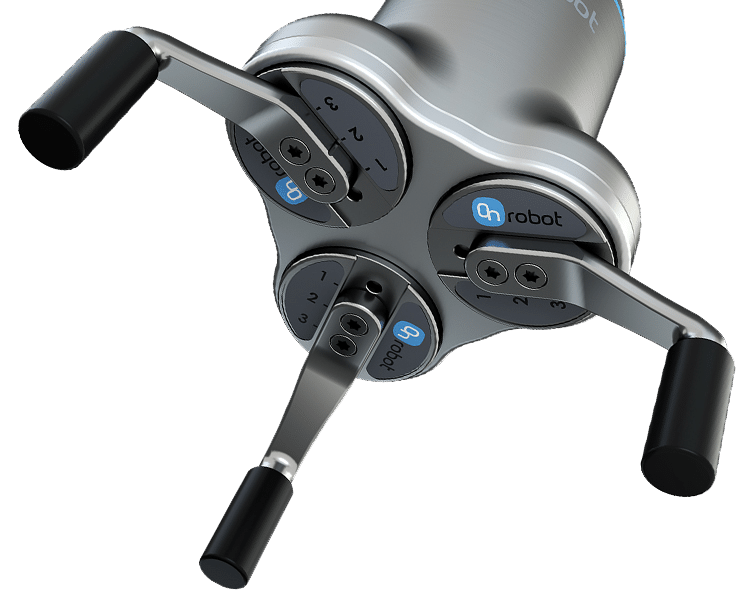
Common Pick & Place Applications:
-
Conveyor picking - from the conveyor into a box.
-
Machine loading – loading an automation cell to increase efficiencies.
-
Connecting machines – transferring products from one process to another.
-
Added value – taking product and adding a laser mark or sticker before packing
3 tips for a
successful pick & place application:
-
Part location – have a designated pick-up location or use vision to pick randomly.
-
Be flexible – secure your investment and build in flexibility from day one.
-
Involve staff – engage your staff and get them on board. The application will see greater success with collaboration!